발루프 자동화 솔루션으로 제재소 생산량 개선
다른 산업과 마찬가지로 제재소의 가장 중요한 목표 중 하나는 생산량 최적화입니다. 큰 차이점은 제재소로 들어오는 나무 품질을 거의 제어하지 못한다는 점입니다. 이상적인 나무의 모양은 원통형에 곧게 뻗어 있습니다. 하지만 각 개별 통나무의 모양은 확실히 다 다릅니다.
구부러지고 원형이 아니며 점점 가늘어지는 통나무가 일반적이고 더 안 좋은 상태의 나무들도 많습니다.
제재소의 목표는 최대한 많은 목재를 생산하는 것입니다. 따라서 제재소는 3차원 (3D) 측정과 1,2차 분해 작업을 위한 고급 장비를 갖춘 고도로 자동화된 공장이 되었습니다. 기본적으로 제재소의 자동화 영역은 아래와 같이 3가지로 나눠집니다:
- 나무에서 최대한 많은 목재를 생산하기 위해 최적의 절삭 패턴으로 3D 측정
- 드라이브 자동화로 나무와 공구 (톱날, 칼, 캔터 헤드 등)을 고속으로 배치하여 처리량 증가
- 통나무 사이 간격을 최소화하기 위해 나무 및 목재 처리 자동화
통나무를 최대한 활용한다는 제재소의 목표를 지원합니다. 최악의 시나리오는 다운타임이 발생하여 전체 통나무가 목재로 가공되는 공정에 직접 영향을 미치는 것입니다. 따라서 전기 엔제니어는 제재소 환경의 문제를 해결해 줄 수 있는 센서를 찾고 있습니다. 센서는 주로 높은 진동과 충격 표준을 충족합니다. 센서들은 열악한 환경에 노출되므로, 센서 보호 하우징은 센서를 통나무와의 충격으로부터 보호하는 역할을 합니다.
원목에서 목재로
제재소에서는 원목을 목재로 효율적으로 가공하기 위해 다양한 크기의 원목을 처리하는 특수 전용 장비를 사용합니다. 그 결과 대형 제재소는 1,2차 분해 구역이 있습니다. 통나무에 상관없이 제재소는 간격을 최소화하고 설정 변경을 피하고자 노력합니다. 이를 통해 목재 가공을 더욱 신속하게 진행하여 공정 속도를 향상 시킬 수 있습니다. 다음은 제재소에서 통나무를 목재로 가공하는 프로세스에 대해 설명해 드리겠습니다.
나무가 제재소에 도달하면 인피드 컨베이어에 인덱싱합니다 (스텝 피더 또는 적재 장비일 수 있음). 유도 센서 중 하나가 스텝을 차례로 배열하거나 자기 변형 위치 센서 (리니어 센서)가 적재기의 단계별 위치에 대한 피드백을 제공하여 적재기의 움직임과 속도를 제어합니다. 통나무가 적재되면 아날로그 거리 센서가 장비 벽 측면에서 통나무 끝까지의 거리를 확인합니다.
이는 통나무가 제재소에 들어갈 때 통나무간에 일정한 거리를 유지하기 위함입니다. 거리를 알면 통나무를 컨베이어에 적재하는 타이밍을 제어하고 간격도 제어할 수 있습니다. 광전 센서인 관통 빔 센서는
1차 분류 - 원목에서 목재 평판으로
제재 (목재 가공)의 첫 번째 단계는 수피를 벗겨내는 박피기를 통과하는 것입니다. 허용 오차가 있기 때문에 선형 센서와 광전식 아날로그 거리 센서가 통나무의 크기를 결정합니다. 통나무의 크기는 박피기의 압력과 속도를 조정하는데 도움이 됩니다. 통나무의 껍질을 제거하면 컷 오프 쇼 (Cut-off shaw) 또는 가로 켜는 톱 (bucking saws) 으로 사전에 지정한 길이로 절단합니다. 다시 선형 센서는 컷 오프 쇼의 모션을 제어합니다.
광전 센서를 쌓아서 통나무 직경을 대략적으로 파악할 수 있습니다. 톱이 작은 통나무를 더 빨리 절단할 수 있기 때문에 속도가 빨라지고 통나무를 자를 때는 느려져야 합니다. 많은 제재소에서 수피를 벗겨낸 통나무를 직경에 따라 "큰 통나무"와 "작은 통나무"로 분류합니다. 그런 다음 특정 통나무 크기에 맞게 설정된 기계로 이동합니다.
20인치 (50cm) 이상 통나무용 송재차
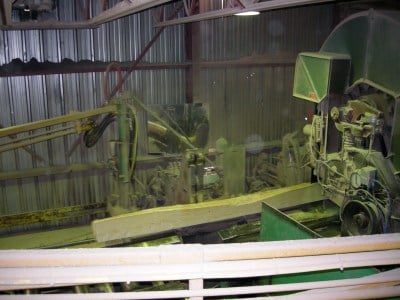
많은 제재소에서는 큰 원목을 많이 운반하기 때문에 송재차를 갖고 있습니다. 선로 형태의 트랙에서 작동하며 하나의 밴드 쏘 (Band Saw)가 있는 송재차입니다. 이 송재차에는 3-4개의 다리가 있으며 여기에는 나무를 고정시키는 클램프와 포지셔너가 있습니다. 자기 변형 센서가 있는 유압 실린더가 나무를 배치하며 극한 주변 환경에서도 이러한 위치 센서는 높은 기계 및 시스템 가용성을 보장합니다. 클램프는 원목이 밴드쏘(band saw)를 통과하는 동안 통나무를 고정시킵니다. 송재차는 원목을 평판 (2개의 평면, 2개의 둥근 측면) 또는 목재 (평평한 면 4개)로 자릅니다.
2차 분해 - 작은 원목을 평판과 경사면으로 분해
작은 원목을 취급하는 제재소는 나무를 2차 분해 장비에 넣기 전에 분해할 필요가 없습니다. 톱으로 자른 후 크기에 통에 분류해서 보관합니다. 스텝 피더는 원목을 컨베이어로 다시 인덱싱하고 스캐너를 통해 소형 원목 라인 기계로 공급합니다. 가능한 많은 양의 생산량을 회수하기 위해 회전 장비는 나무를 최적의 위치로 돌립니다. 칩퍼 장비는 지그 쏘잉이 가능하도록 나무를 중앙에 배치하여 제재수율을 높입니다.
유압 드라이브는 작은 원목 라인을 제어하고 선형 위치 센서로 모든 모션을 제어합니다. 일반적으로 소형 라인은 원목 회전, 센터링, 캔터 헤드로 나무를 잘게 재단, 톱 박스 회전 및 기울이기, 톱 박스 포지셔닝, 프로파일링 헤드와 이젝터로 구성되어 있습니다. 모든 장비는 속도를 염두에 두고 설계되었으며 빠르고 정확한 위치 피드백이 필요합니다. 센서 및 트랜스미터는 강한 충격과 진동을 견뎌야 합니다. 발루프의 제품은 가장 열악한 환경에서도 안정적으로 작동하며 충격 및 진동 테스트를 거쳤습니다.
이동식 톱과 지그 톱
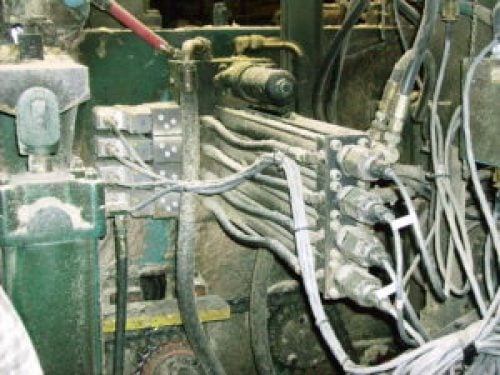
연동 톱 (Gang Edger)과 이동식 톱은 1차 분해 공정에서 나온 목재 평판 및 톱질한 목재를 판자로 자릅니다. 연동 톱 (Gang Edger)은 일정한 간격으로 원형 톱이 있습니다. 이동식 톱은 연동 톱과 유사하지만 톱날 사이의 공간을 변보저 션에 맞게 톱간의 거리를 새롭게 설정합니다.
보정 프로그램은 목재판을 사전 설정하여 피드를 최적화하여 최상의 결과를 이끌어 냅니다. 광전 (레이저) 역 반사 센서는 덕커 테이블을 통과하는 판자를 추적합니다. 공급 위치 실린더 (리니어 센서 내장)는 트리밍 머신에 공급하기 위해 목재판의 위치를 비스듬히 기울입니다.
트리밍, 정렬, 적재, 묶기, 그리고 배송
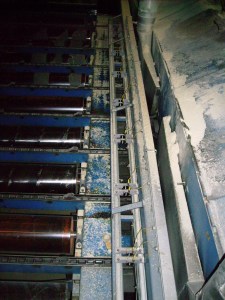
판자가 edgers에서 나오면 창고로 들어갑니다. 다른 스캐너가 판자를 더 작은 판자로 자를 수 있는지 판단합니다. 또는 손상된 경우 판자 품질이 떨어지지 않도록 끝을 잘라야 합니다. 다음 단계에서는 트리밍 장비로 판자를 가공합니다. 트리밍 기계는 최대 12개의 원형 톱이 수평으로 배치되어 있습니다. 이 기계는 긴 판자를 더 짧은 2~3개의 판자로 자르거나 끝을 다듬을 수 있습니다.
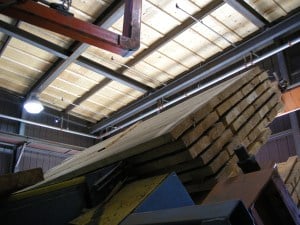
보드가 기계에 들어갈 때 트리밍 기계의 공급 장치에 있는 배경 억제 광전 센서가 하단부를 감지합니다. 그리고 실제 보드 길이를 측정하여 판자가 적절한 사이즈로 재단되었는지 확인합니다. 트리밍 이후 분류기로 이동하여 최종 배송을 위해 끈으로 묶어서 쌓아 놓습니다.
광전식 아날로그 거리 센서는 먼 거리에서 쌓아 놓은 판자를 감지합니다.
발루프 센서가 제재소 자동화를 어떻게 지원할 수 있는지에 대한 추가 정보는 홈페이지에서 확인 가능하십니다. www.balluff.com
원목 대신 베이너판 (합판용 판자)
제재소에서는 원목을 생산합니다. 즉 판자는 한 그루의 나무 중 일부입니다. 다른 유형의 판자로는 베니어가 있습니다. 나무의 얇은 층을 접착제로 붙여서 하나의 판자를 만드는 것입니다. 보통 이러한 층의 두께는 3mm 이하입니다. 선반은 날에 대고 통나무를 지속적으로 돌려서 껍질을 벗겨냅니다. 회전할 때마다 통나무는 더 얇아집니다. 따라서 날 위치를 조정해야 합니다. 선형 센서가 통합된 유압 실린더는 통나무를 중앙에 배치하고 날을 배치하여 수피를 벗겨냅니다.얇은 층을 베니어 프레스에서 접착제로 붙입니다.
휴대용 톱질 장비
궁극적으로 발루프 센서와 트랜스듀서는 대형 제재소뿐만 아니라 이동식 제재소의 자동화도 지원합니다. 자기 변형 또는 자기 센서를 사용하면 오퍼레이터가 톱의 위치를 정확하게 배치할 수 있으며 판자를 정확하고 빠르게 재단할 수 있습니다. Wood-mizer는 글로벌 휴대용 제재 기기를 공급하는 업체로 자사의 기계에 발루프의 자기 변형 센서를 사용합니다. 발루프를 선택한 이유는 제품과 서비스 품질뿐만 아니라 가용성 때문입니다.