시간과 비용에 대한 압박이 증가할수록 표준 공정에 대한 요구가 증가하고 있습니다. 이러한 추세는 생산업체와 공급업체 간의 공급망에도 영향을 끼치며, 최근 몇 년간 이력 추적 (Traceability) 시스템에 대한 중요성이 점점 강조되고 있습니다. 이력 추적 공정의 빠른 구현 및 실행을 위한 한가지 가능한 솔루션은 무선 주파수 인식 (Radio Frequency Identification 이하 RFID) 기술을 설치하는 것입니다.
최소한의 하드웨어와 데이터관리로 생산자재 이력추적
팔레트와 함께 상품이 입고되면, 바코드 스캐너는 kanban 상의 2D 매트릭스 코드를 읽어 들이며 추후 이력 추적 프로세스에 필요한 관련 데이터는 스택의 제품 캐리어의 모든 UHF 트랜스폰더 (K-trays) 에 동시에 전송됩니다. 제품 캐리어 수 (K-tray 수)는 이력 추적 데이터와 함께 저장되며 이 프로세스는 단일 스테이션에서 진행됩니다. 등록 후에 팔레트의 생산 자재는 보호 포장지의 손상 없이 창고로 운송됩니다. 각 트레이에는 하나의 메모리 세그먼트가 있으며 매 시퀀스마다 업데이트됩니다. 컨테이너 데이터베이스는 이동하는 과정에서 생성 또는 확장됩니다.
트랜스폰더에 입고된 제품 데이터를 전송
고객 맞춤형 솔루션으로 기술적 차이를 극복
맞춤형 소프트웨어와 함께 환경 요구 사항을 충족하는 엄선된 트랜스폰더는 각 업체별로 최적화된 맞춤형 솔루션을 제공합니다. 내부 프로세스를 위한 batched part를 준비하기 위해 라벨은 추가 Data Matrix Code ECC 200로 완성합니다.
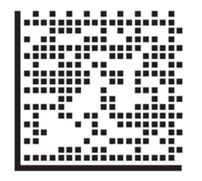
Data Matrix Code ECC 200
2D 바코드는 자재에 대한 암호화된 정보를 수용하지만, 공급업체와 배치 넘버도 포함합니다. 이 중간 과정은 비용과 시간이 많이 드는 조정 작업과 고객에 대한 의존을 피할 수 있습니다.
적재된 팔레트의 자동화된 검토
자재 번호를 기준으로 시스템에는 팔레트 상의 트레이 개수에 표준 로드 정보가 포함됩니다. 결과적으로 팔레트 상의 모든 트렌스폰더가 등록이 되면 자동 스크리닝 작업이 진행됩니다. 등록된 데이터와 예상 데이터 간의 차이가 발생할 경우에는 오류 메시지가 뜹니다. 이러한 오류는 매뉴얼로 수정을 하거나 결함이 있는 태그를 새 것으로 교체하면 해결됩니다
한 개 이상의 RFID 태그에 대한 자동 라벨링
현재 하나 이상의 트레이 상의 트렌스폰더의 동시 라벨링은 UHF 장거리 안테나에 의해서만 구현 가능합니다. 중거리 범위의 안테나의 사용은 0.5 WERP 전송 전력이 적합한 규정된 제한 구역 내에 있어야 하기 때문입니다. 하나의 안테나로 최대 높이 500mm로 쌓아 올린 자재 스택 2개와 400mm 떨어진 곳에 장착된 태그에 레이블을 지정하려면 안테나와 스택 사이의 거리가 최소 250mm 이어야 한다. 만약 거리가 100mm 인 경우 하나의 스택에만 레이블을 지정할 수 있습니다.
UHF 시스템의 주요 장점 :
- 글로벌로 사용하는 표준 인터페이스로 어플리케이션에 문제없이 통합 가능
- 국제 표준 ISO 18000-6C 및 EPC Gen2 Class1 준수
- 데이터 캐리어와 안테나를 결합하여 다양한 적용 가능성으로 인한 유연한 제품 사용
- 최대 6m 감지 거리
- 동시에 다수의 데이터 캐리어 (태그)를 감지
- 버스 인터페이스 및 고급 IT 시스템으로 과거의 제어 시스템에 부착하기에 적합
- 맞춤형 시스템 솔루션 실현
- 다른 어플리케이션에 쉽게 통합할 수 있는 다양한 액세서리 보유
경험에 따르면 RFID 프로젝트는 많은 지원이 필요합니다. 발루프 전문가 팀은 기술 상담 및 지원을 제공해 드릴 수 있습니다. RFID 기술에 대한 보다 자세한 내용은 링크를 참조해 주시기 바랍니다.