1ロットで製造されるバンパーは、協調ロボットの力を借りながらモジュラー方式の生産ラインで製造されています。 ー これが現在の近代的な自動車製造の姿です。透明性と継続的なプロセスなしに、この製造方式は成り立ちません。そのため、信頼ある技術の活用がとても重要です。
多くの自動車メーカーでは、UHFは工場内の製造をコントロールする用途だけでなく、現在では最終仕上げや出荷プロセスで完成車を追跡するための活用が増えています。また、多くの自動車メーカーでは、サプライヤを含める工場を跨いだUHFの活用を始めています。
これにより、ジャスト・イン・タイムとジャスト・イン・シーケンスへの対応がとても容易になります。このブログでは、なぜUHFが自動車製造の未来技術へとなり得るのかをご紹介いたします。
その前にUHFとは?
UHFとはUltra High Frequencyの略で、300 MHz ~ 3 GHzのRFID (Radio Frequency Identification: 無線による自動識別技術) 周波数帯域のことを示します。UHFは、国際規格であるEPC Gen2で運用されており、通常は860 ~ 960 MHzの周波数帯ですが、地域によって定められている周波数帯は異なります。UHFの他に、産業で使用される一般的なRFIDの周波数帯としては、LF(low frequency: 低周波数帯)で使用される125 kHzやHF(high frequency: 高周波数帯)の13.56 MHzがあります。LFは主にTool ID (工具の識別)で使用され、HFはチケットや支払い、製造やアクセス制御などで主に用いられています。
UHFシステムは最大数mの長距離で通信できる性能を持ち、市場でも高速なデータ転送速度を誇ります。そのため、様々なアプリケーションで使用され、RFID市場で最も急成長を遂げています。サプライチェーンの物品や自動車部品の追跡、資産の棚卸し、自動車パーツの照合など、自動車産業だけでも多彩です。
次に動作方法について説明しましょう。UHFのプロセッサは信号を発し、アンテナによってエネルギー周辺へ放出します。UHFタグがこのエネルギーによって起動すると、データ交換が行われます。タグ(別名:データキャリア)は、プロセッサの信号を広報拡散させ、特定のデータ内容に応じて変調します。
UHF vs. 光学システム
インテリジェントなRFIDシステムによって生成されたデータは、効率的なプロセスの透明化にとって貴重な情報です。これを達成するために、革新的なUHF技術の採用が不可欠です。なぜなら、長期的に見ればUHFは既存のHFやLFのRFIDのアプリケーションと同様に光学システムに取って代わる可能性があるからです。この幅広い機能と性能により、UHFは企業間のデータフローを実現する可能性を秘めています。
次の表はUHFが提供する、光学システムでは不可能な性能と相互作用を示しています:
UHFの主な利点
- 最大数mの長距離通信
- 「一括読取り」: 大きな箱の中にある製品たちをゲートやエリアに通すなどして、最大数百の製品を複数で同時に追跡可能
- UHFタグのデータは読むだけでなく必要に応じて変更可能
- 製品へ永続的に貼り付ける、読取り専用の安価なラベルタグ
UHFは物体を識別するために、視野に直接入れる必要はありません。読t取り/書込み範囲にあるだけで良いです。販売や出荷のために商品が梱包されていても運用できます。
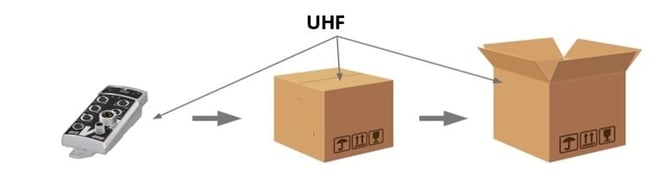
たまに必要とされる短距離通信
もちろん、UHF技術で短距離の読取りは可能です。これは、イントラロジスティクスまたは物流の一部で要求されます。しかし、これは特定の正常領域に取っては課題となり得ます。部品製造では検出範囲を限定し、付近にある製品は認識せずに1つの部品だけ検出できることが求められます。ここで重要なのは、1回の検出で1つの部品が検出されるようパワーを下げるか、短距離に特化したUHFプロセッサとアンテナを採用することです。
UHFは自動車産業のサプライチェーンを前へ押し進む唯一の方法
UHF技術の可能性は、製造工程全体に渡ってこの技術に対応していなければ十分に発揮できません。UHFの活用は汎用性が高いため、UHFタグが製造工程内に留まるクローズドループと、UHFラベルが車体やバンパー、ヘッドレスト、タイヤなどの部品に永続的に貼り付けられるオープンループの両方に適応できます。
またその他にも、マニュアル作業を削減するだけでなく、倉庫を完全見える化(と自動化!)することにより、在庫の削減や在庫不足の防止に貢献します。これにより、あなたのビジネス全体を向上させます。また、特定領域へ安全にアクセスすることもできます。
また、UHFに頼るもう一つの理由は一貫してデータ品質の水準が高いことです。すべてのエリアで同じデータタイプを取得することで、読み比べにより傾向分析を行うことができます。そのため、異なる技術の組み合わせでは不可能な、生産プロセス全体に関する幅広い情報を得ることができます。これより、常に状況に応じて対応するのではなく、予防策を講じるチャンスを得ることができます。