Improving sawmill yield through automation
It is not a surprise that optimizing yield is one of the most important objectives in a sawmill (or lumber mill) as it is in any other industry. The big difference is that there is hardly any control over the quality of the logs that enter the sawill. In the ideal world all logs are not only cylindrical in shape but also straight. But obviously each individual log is unique in shape.
Crooked, out-of-round, or tapered logs are common and even worse: usually it is a combination of these shapes.
Still the target is to recover as much yield from each log as possible. Therefore sawmills turn into highly automated factories with three dimensional (3D) measurement of logs, and advanced equipment for primary and secondary breakdown. Basically there are three areas of automation in a sawmill:
- 3D measurement for optimum cutting pattern to recover most yield from a log
- Automation of drives to position the log itself, or tools (e.g. sawblades, knifes, canter heads…) at high velocity to increase throughput
- Automation of log and lumber handling to minimize the gap between the logs
All of the three areas support the sawmill’s target to get the most out of the logs at the highest speed. The worst case is any downtime as it directly impacts the whole log to lumber process. Therefore electrical engineers look for sensors that meet the challenges of the sawmill environment. Mainly sensors must meet high vibration and shock standards. As they are exposed to the environment, protective housings help to protect the sensors from logs crashing into them.
From logs to lumber
To efficiently process logs to lumber, sawmills use dedicated equipment for different sizes of logs. As a result bigger mills have a primary and a secondary breakdown area. Independent from the logs, sawmills aim to minimize the gaps and to avoid changes in the setup. This allows them to run faster and to increase the production rate. Here is the process how a log turns into lumber in a sawmill.
When a log arrives at the mill it is indexed onto the infeed conveyer (could be a step feeder or log loader). Either inductive sensors sequence the steps. Or a magnetostrictive position sensor (linear transducer) provides feedback of the step position of the loader to control motion and speed. Once the log is on the loader analog distance sensors determine the distance to the end of the log from the side of the loader wall.
This is to ensure a constant distance between the logs (log gap) as they enter the sawmill. Knowing the distance enables them to control when the log is loaded on the conveyor. And thereby they can control the gap. As an alternative photoelectric a thru beam sensor determines if a log is present for the final two steps on a loader. These sensors work with a long measuring range. Additionally they have a large functional reserve and are very resistant to dirt and dust.
Primary breakdown – from raw log to slabs and cants
The first step of the log is to run through a debarker that removes the bark. As there are tolerances in shape, linear transducers and photoelectric analog distance sensors are used to determine log sizes. These sizes help to adjust the debarker’s pressure and speed. After debarking the logs are cut to the best pre-determined length by cut-off or bucking saws. Again linear transducers are used to control the motion of the cut-off saw swing.
By stacking some photoelectric through beam sensors they can be used to determine the log diameter roughly. This leads to increasing speed as the saw can cut through smaller logs faster and has to slow down for larger logs. Many mills just sort their debarked logs into “large logs” and “small logs” based on their diameters. And then go into machines that are set up for those particular log sizes.
Log carriage for 20″ (50cm) logs and more
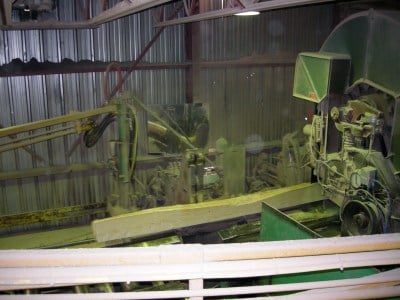
Many mills also run a lot of larger logs and therefore have a log carriage. This is a single band saw with a carriage that runs on railway style tracks. The carriage has three or four knees that have positioners and log clamps (dogs) that hold the log. In the knees hydraulic cylinders with magnetostrictive transducers position the log. Even under extreme surrounding conditions, these position sensors guarantee a high machine and system availability. The clamps hold the log while it moves through the band saw. The carriage cuts the logs into slabs (two flat, two rounded sides) or into cants (four flat, square sides).
Secondary Breakdown – from small logs, slabs and cants to lumber
Mills that run smaller logs do not have to break down the logs prior to putting them through the secondary breakdown equipment. After the cut-off saw, the small logs will be sorted by size into bins. Step feeders index them again onto a conveyor and that feeds them through a Scanner into the small log line machine. To recover as much yield as possible log turners turn the logs in the optimum position. Chipper canters center them to enable curve sawing, which leads to increased lumber recovery.
Hydraulic drives dominate small log lines and all motion control happens with linear position transducers. Typical small log lines consist of log turning and centering, chipping with canter heads, saw box slew and skew, saw box positioniers, profiling heads and outfeed pickers. All of the equipments’ design aims for speed and therefore they require fast and accurate position feedback. Sensors and transducers must withstand high shock and vibration. Balluff’s products survive even in toughest environments and undergo intensive shock and vibration testing.
Shifting edgers and curve sawing
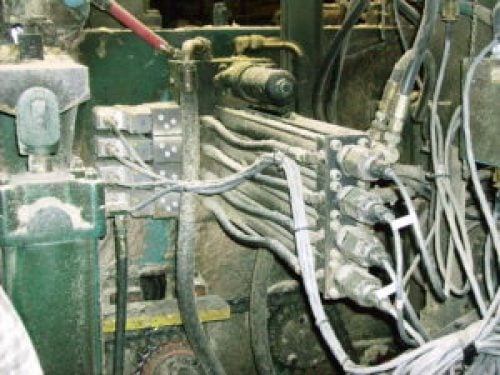
Gang edgers and shifting edgers cut cants and slabs from the primary breakdown into boards. Gang edgers have circular saws stacked at fixed spacing. Shifting edgers look similar to gang edgers except that they change spacing between saw blades can be changed. Therefore each saw is connected to a hydraulic positioner. A scanner looks at the cant or slab and determines the best solutions of cuts to produce best results. After the scanner the positioners of the shifting edgers set the new saw spacing to match that solution.
Edger optimizers pre-position the board and optimize the infeed to get the best payback from the machine. Photoelectric (laser) retroreflective sensors track boards through the ducker table. The in-feed position cylinder (with integrated linear transducer) skews the board in the best position to be fed in the edger.
Trimming, sorting, stacking, strapping, shipping
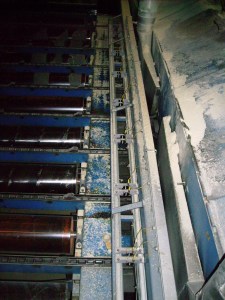
The boards go into bins when they come out of the edgers. Another scanner determines if the board can be cut down into shorter boards. Or if a damaged end needs to be cut off so that the board is not graded lower. The next step is processing the board through a trimmer. The trimmer is a set of up to about a dozen circular saws positioned across the conveyor. It can cut longer boards down into two or three shorter boards or just trim the ends.
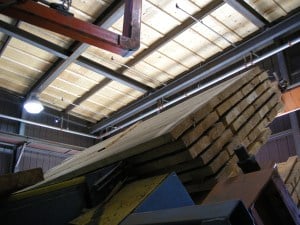
Background suppression photoelectric sensors at the infeed of the trimmer look down at the board as it goes into the machine. And they determine if the board is actually as long as the scanner information indicates. The same sensors confirm after the trimmer that the board was cut down to the proper size. After the trimmer they go into a sorter and and from there to stacking and strapping to final shipment.
We provide additional information how our sensors help to automate sawmills on our website.
Veneer instead of solid wood
A sawmill produces solid wood. This means that the board is out of one piece of wood. Another type of boards is veneer. This means that thin layers of wood are glued together to reach a board. Usually these layers are less that 3 mm thick. A lathe continuously turns a log against a blade to peel it. With each rotation the log becomes thinner. Therefore the blade position needs to be adjusted. Hydraulic cylinders with integrated linear transducers center the log and position the blade to peel the trunk. The thin layers are glued together in a veneer press.
Not only stationary, but also portable sawmills
In the end our sensors and transducers not only help to automate huge mills, but also portable sawmills. Magnetostrictive or magnetically sensors enable operators to exactly position the saw unit. So they achieve accurate and fast cutting of boards. Wood-Mizer is a world leading supplier of efficient and fast portable sawmills that uses magnetostrive position sensors in it’s machines. The reasons for Balluff are its product and service quality as well as the availability.