Optoelectronic sensors with laser and red-light are widely used in all areas of industrial automation. A clean, dust-free and dry environment is usually essential for proper operation of photoeyes. However, in many dirty and harsh applications are optical sensors the best principle of choice. This is for instance the case in many application in steel mills at the raw-steel production, further metallurgical processes down to casting and hot-rolling. Beside already mentioned factors, there is in many cases extreme heat present in steel and metal production.
Optical Allrounders
One outstanding feature of photoelectric sensor compared to other operation principals, is their long sensing distance. Also special is the ability to detect objects independant of their material. Inductive sensors usually operate on short distance and are best to detect metal objects. Capacitive sensors recognize different materials at larger distance, but they could be interferred quite easily from residual media like liquids or moisture. Standard capacitive sensors can be activated even by touching with your finger.
Beside a wide variety of different applications which can be solved by photoeyes, optical sensors are used as well for safety relevant functions.
Operation of sensors at high ambient temperatures
In steel production many parts of the process are accompanied by high ambient temperatures. Liquid steel and iron have temperatures between 1400°C (2552°F) up to 1536°C (2797°F).
Material temperature during continuous casting and hot-rolling are still between 650°C (1202°F) and 1250°C (2282°F). This is visible and can determined by steel color charts.
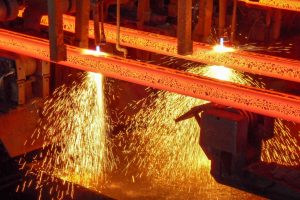
Usually photoelectric sensors are specified to work up to ambient temperatures of 55 to 60°C (131-140°F). This maximum temperature is limited mostly by specs of the optical components of the sensor like laser-diodes.
Now you could assume that it is not recommended to operate photoelectrical sensor in such kind of harsh environment. I will introduce some methods how to make sure your optical sensors will operate reliable despite nasty conditions.
Detecting glowing metals
First of all should be provided that the material temperature of the target you want to detect has a temperature below 600-700°C. If you want to detect reliable red-hot or white glowing steel parts with temperatures beyond 700°C (1292°F), this won’t work with standard laser- or red-light sensors. Red-hot steel is emitting light at the same wavelength than it is used by optoelectronic sensors. This can interfere the function of the sensor.
In such applications you need to use sensors which operate based on infrared light. This pyrometer or infrared-temperature sensors are a topic in another blogpost.
How can you operate optoelectronic sensors reliable in harsh environment?
There are different ways to ensure reliability and lifetime of optoelectronic sensors under extremely harsh conditions:
- Higher distance from the target object
- Regular cleaning
- Use of optical glass fibers
- Cooling of sensors
- Mechanical protection of the sensor
One major advantage of photoelectronic sensors is the long range, which enables us to install them with a certain distance to the target object. The impact of heat emission of the detected object can be reduced siginificantly in this way. Very often the remote mounting will make the sensor operating at room temperature. However, in hot regions this ambient temperature in steel production can be even up to 50°C (122°F).
If you intend to detect quite small objects with high precision, the maximum distance for the installation might be limited. For this purpose chemical resistant glass fibers are suitable and can handle temperatures up to 250°C (482°F). These pre-fabricated fiber optic assemblies can be easily attached to the sensor. The sensor itself can be mounted on a cooler and protected place.
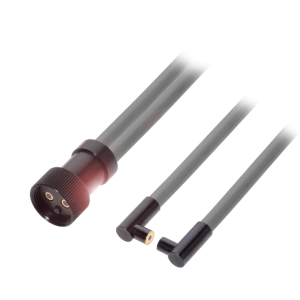
Cooling of optoelectronic sensors
The use of water cooling at sensors in steel manufacturing can be critical. Beside cost for instrumentation air or clean cooling water there are also safety aspects. Water cooled sensor protection housings are expensive and bulky compared to the contained sensor. Leaks or water spry due to a bursting water hose can be dangerous.
Therefor it is recommended to take a closer look, where to use and install photoelectrical sensors:
- Which distance to the hot object and sensor can be realized?
- What is the maximum temperature at this location?
- How long will be the duration of extended heat during normal operation and at breakdown?
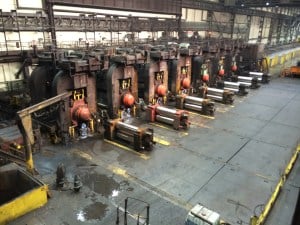
Hot-rolling of flat steel
At many locations in the steel production process, we face extensive heat just temporary. In the hot rolling mill, a slab runs through a rougher mill multiple times before it continues to a multi stage finishing mill stand to be rolled to the final thickness. After that the metal strip runs into the coiler to be winded up.
This process runs in sequence, the glowing material is for a limited time present at each stage of production. Until a new slab runs out of the reheating furnace, temperatures have normalized again.
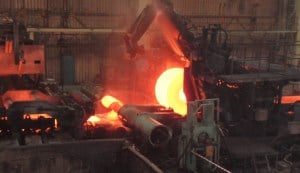
Often standard sensors are used here and they are running well. But when there is a production stop for any reason, the process will be interrupted. In this case it is possible that the hot material just stop in front of a sensor. Due to a temporary temperature overshoot, a sensor can be damaged like shown in this picture.
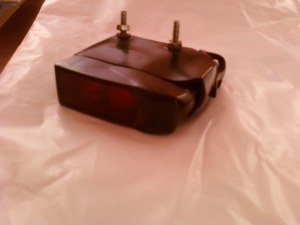
Protective housing accessory
To protect optoelectronic sensors against temporary overheating, we developed this universal protective enclosure.
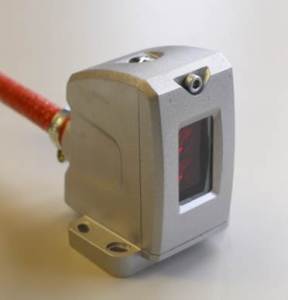
Additional protection can be achieved when a heat resistant sleeve is used around the cable. This sleeve can be attached directly to the cable gland.
This housing made of die-casted aluminum provides mechanical protection to the sensor, which has in many cases a plastic housing. The window to the sensor consists of glass or PMMA.
On the other hand, this housing acts as a thermal protection against heat.
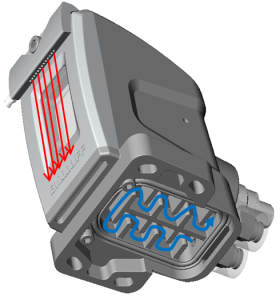
Heat protection without additional cooling
We have exposed the housing with a sensor to temperatures up to 160°C/320°F. The test was performed in an oven where the temperature impact was from all sides. In many real applications, the temperature impacts the sensor location just from one direction.
Without additional cooling the inside of the housing was heated up to 60°C/140°F after aproximately 4-5 minutes. So the maximum specified operating temperature was reached after a quite short time. If you have to consider a longer duration of a heat impact, it is recommended to use additional cooling.
Optional cooling with air or water
A first test with air, where the inside of the housing was flushed with up to 35l/min., could bring down temperature just around 5K (room temperature 23°C).
With this experience, we do not recommend cooling with air since it is not efficient. You can still apply compressed air to the pre-defined points on the outside of the housing, but it will not provide efficient temperature reduction. Static air pressure at this point can improve IP protection. Due to the pressure inside the housing there can not enter moisture or liquid to the inside.
We could use a remaining area in the bottom part of the housing, to accomodate cooling channels, which are covered with a cap and sealing (optional). Here it is possible to connect water.
Another test showed, that it was possible to reduce the temperature inside the housing at 100K with a flow of water at 2l/min and a water temperature of 8°C (normal water tap).
By using this small amount of water, a standard sensor can be operaded at ambient temperature of up to 160°C continuously. In case of a temporary overheating e.g. during a machine breakage, the temperature of the sensor can be stabilized by providing cooling agent or can be even reduced.
At 160°C housing temperature, the sensor could be cooled down within 15 minutes to its maximum rating of 60°C. (8°C water temperature, 2l/min flow).
Basically, it would be suficient, when the water cooling is activated just in case of an emergency situation to protect the sensor.
Main features of the protective housing:
- Protection for heat, dust and moisture
- IP67 protection (with cable sleeve IP69K)
- Durable die-casted aluminum housing
- Glass or PMMA screen (Front part with screen available as spare part)
- Optional air-blower to keep off dust
- Quick and easy mounting and replacement of the sensor
- Cable gland for protective sleeve
- Optional water cooling (continuously up to 160°C/320°F)
- ATEX-Approval for the glass-version (Zone 22)
- 2 sizes (BOS/BOD23K & BOS50K)
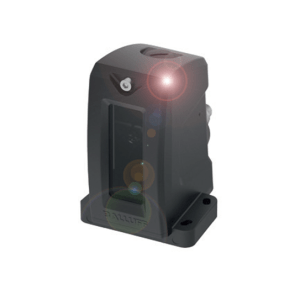
Here you find an overview on available protective enclosures